Les informations ci-dessous sont issues d’un article écrit par deux enseignants chercheurs du pôle MAS. Cet article est paru dans les Techniques de l’ingénieur M3320 et s’intitule « Procédés de frittage PIM ».
ASPECT THÉORIQUE DU FRITTAGE
EQUIPEMENTS ET ATMOSPHÈRES UTILISÉS
EXEMPLES ET CONDITIONS TYPIQUES DE FRITTAGE DE DIFFÉRENTS MATÉRIAUX
Le cycle de frittage, qui se décompose typiquement en différentes séquences de montée en température et de paliers, est une étape cruciale afin d’obtenir une pièce finale de qualité. Comme nous venons de le préciser, tous les paramètres de ce traitement thermique, qu’ils soient inhérents au four (type de four, supports, éléments chauffants…) ou non (temps, température, atmosphère…) doivent donc être parfaitement maîtrisés puisqu’ils influenceront la microstructure des pièces et donc leurs propriétés. Déterminer l’ensemble des paramètres pour obtenir une pièce finale de qualité est donc une étape difficile à mettre au point. Notons que cette mise au point se fait généralement de façon empirique puisqu’il n’existe pas de conditions de frittage génériques pouvant s’adapter à l’ensemble des matériaux.
Matériau | Température de frittage | Atmosphère | Durée du palier de frittage | Remarques |
Alumine | 1600-1700°C | AirouH2 | 1 – 4 heures | Utilisation possible de MgO, NiO pour freiner le phénomène de croissance des grains. La présence d’impuretés telles que le carbone est à proscrire car elles limitent la densification. => Etape de déliantage primordiale |
Zircone | 1100°C-1500°C | Airou H2 | 1 – 2 heures | Utilisation d’oxydes (d’yttrium, de magnésium ou de cérium) pour un meilleur contrôle de la microstructure. |
Nitrure de silicium | 1600-1800°C | N2 sous une pression d’1 atm minimum | 1 – 5 heures | Utilisation d’oxydes (d’yttrium, d’aluminium ou de magnésium) pour un frittage en phase liquide permettant une meilleure densification. |
Carbures de tungstène (WC-Co par exemple) | 1350- 1450°C | Vide | 1 heure | Utilisation de four en graphite pour réduire le phénomène de décarburation. Une pression peut être appliquée en fin de cycle pour fermer la porosité. |
De même, pour une nuance de matériau prédéfinie, ces conditions peuvent varier en fonction de la qualité chimique et de la réactivité des poudres. Ainsi des pièces frittées dans des conditions identiques à partir de poudres inox préparées par atomisation par gaz ou par eau ne présentent pas les mêmes caractéristiques . Les pièces à base de poudre atomisée par l’eau frittent en général plus difficilement du fait, probablement, d’une plus grande quantité d’oxyde qui limite le contact entre les particules et qui réduit donc la réactivité des poudres lors du frittage. Comme nous l’avons déjà souligné, ces couches d’oxyde forment une barrière au frittage en empêchant les atomes de diffuser librement. De façon générale, les poudres métalliques sont très sensibles à la présence d’oxygène, source de formation d’oxyde, l’étape de frittage doit donc être réalisée sous atmosphère réductrice ou sous vide. Notons aussi que certains matériaux sont particulièrement sensibles au phénomène de fragilisation par hydrogène, comme par exemple le titane, le tantale, il est alors recommandé de fritter sous vide ou sous gaz inerte.
Plusieurs études ont aussi montré l’influence de la taille des poudres. Les poudres de granulométrie faible frittent plus rapidement du fait d’une surface spécifique plus importante. Ainsi, dans le cas des céramiques (alumine, zircone), l’utilisation de poudre submicronique est privilégiée, car elle entraîne une meilleure densification à température plus faible. Même s’il est donc difficile de donner toutes les conditions pour un frittage optimum, les tableaux présentent quelques exemples typiques de conditions de frittage pour certains matériaux utilisés classiquement en PIM . Ces conditions ne sont données ici qu’à titre illustratif puisque nous venons de voir que les paramètres de frittage peuvent évoluer selon notamment la taille des poudres utilisées, les microstructures souhaitées…
Matériau | Température de frittage | Atmosphère | Durée du palier de frittage | Remarques |
Acier | 950-1250°C | N2MélangeH2/ N2(5/95%)ou H2/ Ar | 1-2 heures | Addition de Cu, Ni, B pour aider à la densification en améliorant notamment les phénomènes de diffusion (par exemple en mettant en présence une phase liquide). |
Acier Inoxydable | 1350-1400°C | H2 ou vide | 1-4 heures | Une attention particulière doit être portée afin d’éviter les contaminations de carbone et d’oxygène. |
Titane et alliages de titane | 1100-1450°C | Vide (ou H2 pour les hydrures) | 1-4 heures | Pas d’utilisation de substrats en graphite ou alumine car ils réagissent avec Ti à haute température.Utilisation d’oxyde de zirconium ou d’yttrium pour substrat. |
Cuivre et alliages de cuivre | 950-1050°C | H2 ou mélangeH2/ N2 | 30 min-1heure | L’addition de Fe, Cr, Al ou d’autres éléments pouvant former des oxydes stables, est efficace pour éliminer la contamination par l’oxygène. |
QUELQUES DÉFAUTS TYPIQUES DE FRITTAGE
L’un des principaux problèmes rencontrés durant le frittage est lié aux gradients de température existant dans les fours, notamment près des portes, ou encore des buses d’arrivée de gaz, provoquant alors des hétérogénéités dans la pièce finale. La pièce peut alors présenter des zones plus ou moins frittées (présence de pores par exemple) ou être hétérogène au niveau de la taille des grains.
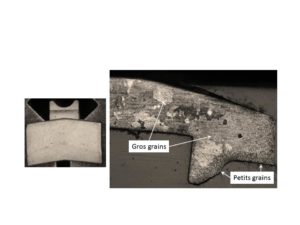
Rappelons que les propriétés mécaniques des matériaux métalliques et céramiques sont notamment conditionnées par ce critère. Au niveau macroscopique, ce gradient de température, peut aussi entraîner des distorsions.
Ces distorsions peuvent aussi intervenir à cause des forces de gravité, ou encore des frictions entre le support et la pièce . Pour éviter les déformations dues à la gravité, il faut limiter les parties de la pièce ne pouvant être soutenues par le support lors du frittage, notamment si elles sont minces. Lorsque cela est possible, l’une des solutions à ce problème consiste à modifier la forme de la pièce en ayant recours à des faces de référence (tels que des méplats) pour le frittage ou de tenter d’augmenter la rigidité de la pièce. L’utilisation de supports moulés adaptés peut aussi être envisagée, même si cette solution est souvent plus coûteuse.
La densification peut aussi être entravée par la présence de porosité, dite fermée. Il existe deux types de porosité : ouverte ou fermée. La porosité est définie comme ouverte lorsque le réseau de pores est interconnecté, ou fermée lorsque les pores sont complètement isolés de la surface de la pièce et d’un réseau de pores interconnectés. La porosité fermée peut être relativement difficile à éliminer. En effet, lorsque les pièces sont frittées en présence d’un gaz, celui-ci est progressivement expulsé de la pièce au fur et à mesure de la densification. Lorsque le gaz se retrouve piégé dans un pore fermé, et que les atomes du gaz ne peuvent pas diffuser dans la phase solide du matériau, la pression interne augmente progressivement (du fait du rétrécissement du pore) jusqu’à atteindre un certain équilibre. Cette porosité fermée, remplie alors de gaz sous pression, entrave la densification complète et peut entraîner une déformation. Dans certains cas, des pièces cloquées ou explosées peuvent être observées. Ce phénomène n’est pas rencontré lorsque le frittage est effectué sous vide ou en présence d’hydrogène puisque la diffusivité de ce dernier est assez grande pour permettre la diffusion du gaz à travers la phase solide métallique ou céramique.
De par la nature même du procédé PIM, des difficultés spécifiques supplémentaires doivent être prises en compte vis-à-vis du frittage classique. Comme évoqué précédemment, la contamination par le carbone est un problème inhérent au procédé du fait de la présence du liant. En conséquence, les taux de carbone résiduels après l’étape de déliantage doivent être parfaitement contrôlés car ils peuvent avoir de lourdes conséquences sur la microstructure et donc sur les propriétés finales mécaniques de la pièce.
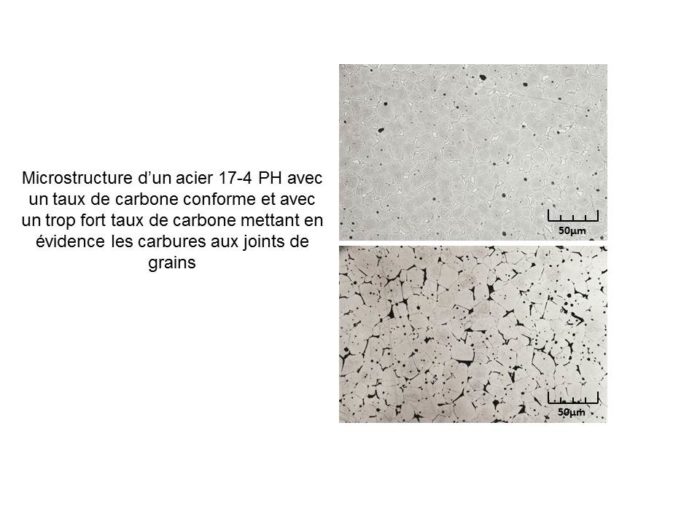
En fin de frittage, certaines pièces présentent en leur sein des retraits anisotropes qui peuvent amener à des fissures. Ce type de défaut est directement relié à des gradients de densité. Rappelons que le retrait est inversement proportionnel à la densité de charge. Plus la densité de charge sera élevée, moins le phénomène de retrait sera important. Ces gradients de densité sont souvent présents dans la pièce verte (après l’étape d’injection) et sont dus, comme nous l’avons déjà indiqué, à une ségrégation poudre-liant. Cette ségrégation peut être inhérente au feedstock ou apparaître lors de l’injection avec des taux de cisaillement trop importants ou lors du déliantage par effet de capillarité par exemple. Imaginons une zone où la densité de charge est faible et où les particules ne sont pas directement en contact, les cous de frittage ne peuvent alors se former. En conséquence, une zone non frittée ou même une fissure peuvent apparaître.
Exemple de zone non frittée. Les grains de poudre initiaux sont visibles au centre de la photo obtenue par microscopie électronique à balayage.